Blog
Solving puzzles is the best part of the job
Kirsten Koreman – Lekkerkerk, Process Engineer Kirsten (29) has been working at Bos Nieuwerkerk for five and a half years now. She started as a working student and, after completing her Mechanical Engineering studies, seized the opportunity to prove herself as a Process Engineer.
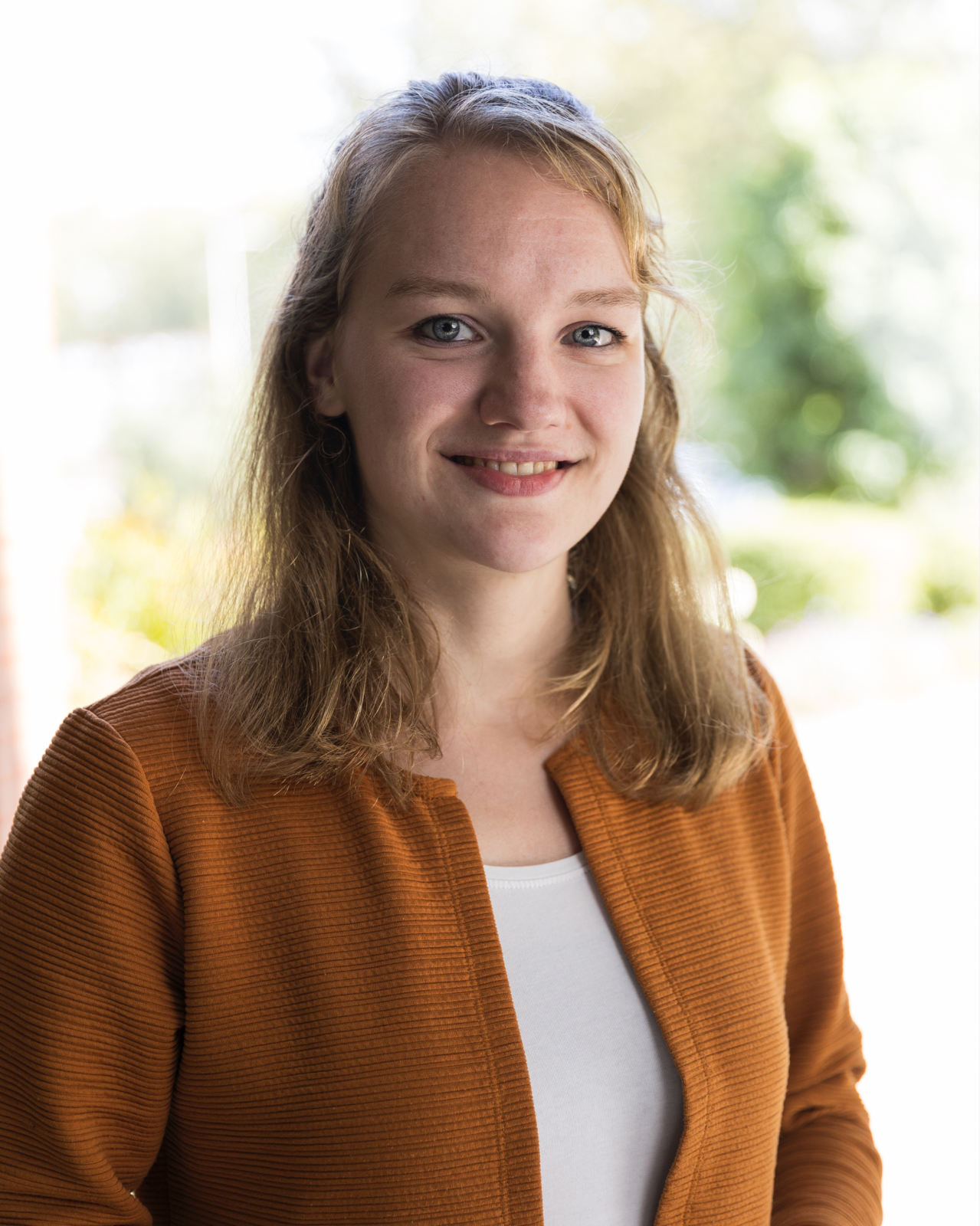
“I studied Mechanical Engineering at Delft University of Technology, including a master’s in Transport, Engineering & Logistics. Since internships weren’t part of the curriculum, I looked for a place where I could get a taste of the professional world. At the time, I had a part-time job at Praxis, but I suspected there had to be work more closely related to my studies. I was still living with my parents in Nieuwerkerk, so I decided to bike around the local industrial area, note down company names and reach out to a few. Bos Nieuwerkerk replied right away—enthusiastically. That already told me something about the company. The conversations that followed confirmed my gut feeling: this was a great team with a lot to offer.”
What kind of work did they have in mind for you?
“Drawing. In 2D, 3D, cutting and standard drawings. I graduated in 2020. Due to COVID, I had to give my final presentation online, but my direct colleagues joined the call, which was really nice. Not long after, they offered me a job as a Process Engineer. It felt like the perfect role for me, so I said yes. In this position, I work on improving internal processes. That saves us time—time we can use to focus on customer-specific details, which in turn raises the quality of our output.”
We record our knowledge in parametric models.
Are you involved in all internal processes or just the engineering process?
“Actually, all internal processes. About two years ago, I mainly focused on the engineering side, because we were transitioning to a new CAD system. That involved capturing our knowledge in parametric models, so we wouldn’t have to start from scratch for every new design. In the ERP team, I’m the project lead. In Q1 of 2024, we’ll be switching to a new ERP system that will help us store and retrieve information more efficiently, and also streamline communication between departments. Together with a consultant, we made a selection, and now we’re customising the system to fit our needs.”
Is setting up an ERP system something you enjoy?
“I really enjoy it. Now that we’ve launched a test environment and people can see the value of it, it’s really starting to come alive internally. The goal is to set up an ideal workflow and anchor it in our ISO certification. That way, we also commit ourselves to working in this way. At the same time, we want to avoid creating a system that gives you a ‘computer says no’ response at the slightest deviation.”
What do you enjoy about building parametric design models?
“I love spotting patterns, and parametric design really taps into that. In our design process, we often deal with recurring parts and actions. With parametric design, we bundle all our knowledge into an over-complete model. For each project, our engineers only need to enter a few parameters. Anything you don’t fill in drops away automatically, and what remains is your design.”
The ultimate goal is a parametric model of a complete chimney.
Do you already have parametric design models in place?
“Yes, we’ve created several models for chimney components, like a base, a side connection, a top section and a basic duct. The ultimate goal is a parametric model for an entire chimney. Since I don’t have enough time to develop this myself, I proposed bringing in a specialist to help us—and that’s what we’re going to do.”
Do you also work on improvements in the workshop?
“No, not yet. But we do have a team exploring opportunities for robotisation. I did kick off a small project in the workshop, though. A sales colleague visited a client who told him they had stopped using disposable cups. On the way back, that got him thinking about our paper usage, and he asked me to take a look at it. We don’t use disposable cups ourselves, but I am now exploring how we use paper and packaging materials—even in production—to see where we can reduce waste.”
What’s your take on the company?
“It’s a wonderful family business that truly puts people first. About six months after I started here, my mother-in-law became seriously ill and eventually passed away. The only message I got from my colleagues was: ‘Take your time.’ There was no pressure, only understanding. We support one another. When someone has a baby, Martine, Miranda and Bianca will visit the new parents. We celebrate birthdays and wedding anniversaries together. Sometimes a grandchild will drop by and you’ll see a tough grandfather melt into a softie. And every time we land a big order, there’s cake—and in my case, a cake that’s specially made to suit my dietary restrictions.”