Blog
“What these companies offer is pretty unique”
Project manager Sidney Bakker found his way to Bos Nieuwerkerk after an extensive search, both in the Netherlands and abroad. As it turned out, the company was one of the few able to deliver exactly what his client needed—while also being flexible and collaborative.
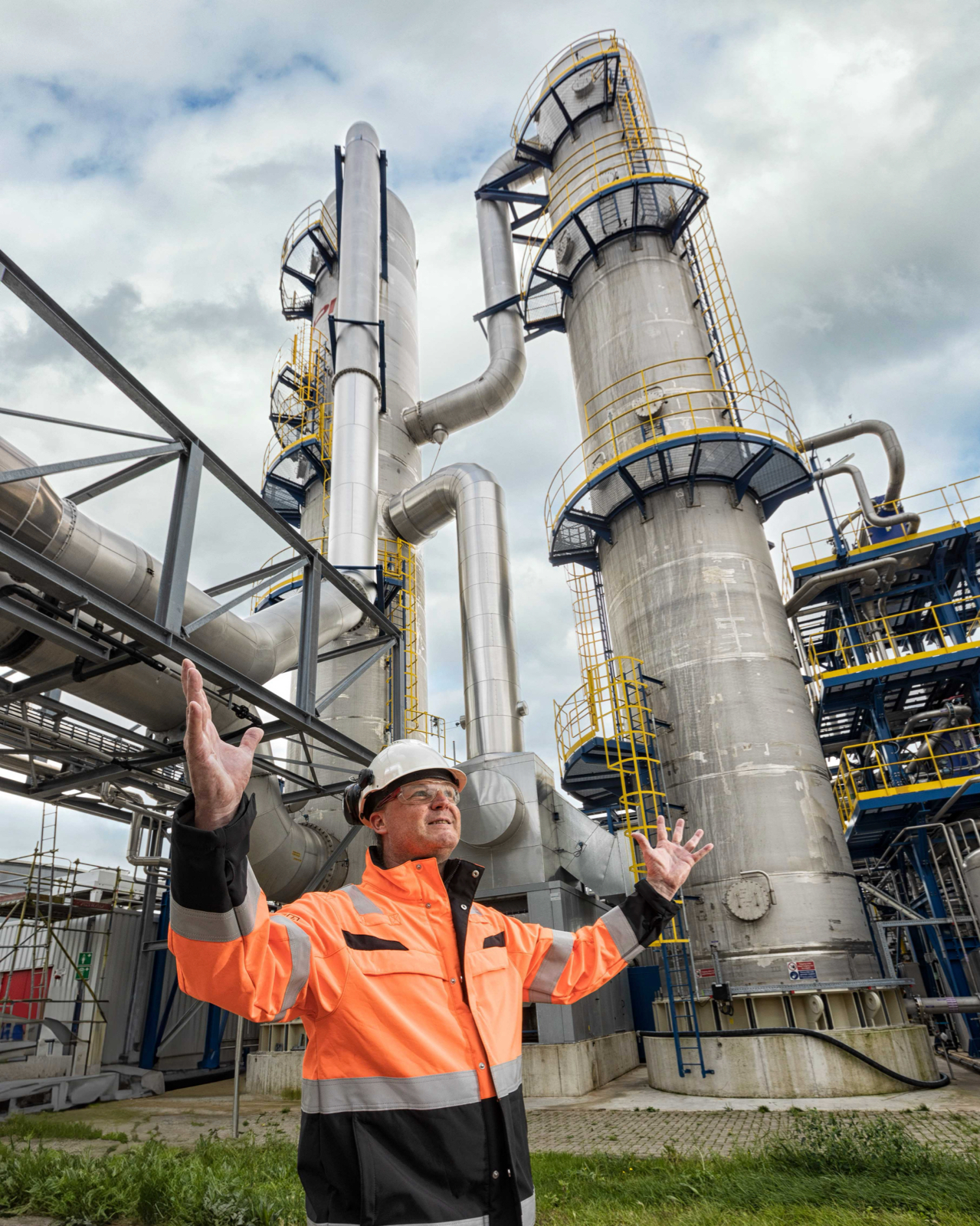
Sidney, how did you first come into contact with Bos Nieuwerkerk?
“About five years ago, we were looking for a company to install the ducting for the flue gas supply and return lines for a CO₂ capture system at AVR Duiven. This involved connecting to the existing plant. The job concerned warm flue gases at low pressure, coming from the incinerator. That doesn’t call for heavy-duty piping or overengineered materials—a sort of ‘horizontal chimney’ would be enough. The catch is that warm flue gas can cool and condense, which can cause corrosion issues. It wasn’t easy to find a partner who could handle that.”
Was no one offering the solution you needed?
“None of the companies we knew. There are plenty of firms that install gas pipelines, but they usually deal with high pressure. Others install ducts for ventilation systems, but those operate at low temperatures. In short, there are very few companies that can build large flue gas systems for high-temperature applications. We had to search far and wide. In the end, we found a few options, but Bos Nieuwerkerk was clearly the most collaborative and solution-oriented.”
How did the collaboration go?
“Really well. Bos Nieuwerkerk came prepared with multiple design options, which immediately inspired confidence. That gave them an edge over the competition. We stayed in close contact throughout the project, which was great. The location where the ducts had to connect to the CO₂ installation changed several times, and each time Bos Nieuwerkerk came up with new solutions—tirelessly. And what I really appreciated: they didn’t immediately bring up additional charges, which many companies tend to do. Connecting to the existing chimney was another big challenge, and they handled it perfectly.”
Did you work with Bos Nieuwerkerk again after that project?
“Yes, but that time the project started through Heat Matrix. I didn’t even realise at the time that the two companies were already working closely together. There are a lot of incineration plants releasing hot flue gases. It would be great if this heat could be recovered and reused—say, to reduce natural gas consumption. But companies are often hesitant, because flue gases can contain SO₂, NO₂, and CO₂, which can form acids when they cool and condense. That’s why you need ducts and heat exchangers that can withstand that environment. Heat Matrix specialises in this. They explore different ways to minimise the risk of acid corrosion. I’m now in touch with several suppliers in the sulphuric acid industry who are very curious to learn how they do it, because they too are hesitant to recover heat from their flue gases due to corrosion concerns.”
With Bos Nieuwerkerk for the flue gas ducting and Heat Matrix for the heat exchanger, you have one single point of contact for the design, manufacture and installation of a complete system.
So Bos Nieuwerkerk and Heat Matrix are breaking new ground?
“That’s right. Heat Matrix has already completed several feasibility studies that show this is not only possible, but also economically viable. Especially with rising gas prices, the payback period is getting shorter. With Bos Nieuwerkerk handling the ducts and Heat Matrix providing the heat exchanger, you have a one-stop shop for a full turnkey solution. I completely understand why the two companies have now merged. Besides the synergy it creates, they also share the same culture. I’m convinced both companies have an exceptionally high rate of repeat business—because helping the customer is truly their top priority.”
Are you currently working on other projects involving Bos Nieuwerkerk?
“Yes, I’m now working as a Cost Engineer for a client that selected Bos Nieuwerkerk to install a chimney. When I heard that, I was able to say with full confidence: ‘Then you’re in good hands.’ And that’s exactly how it turned out. The project manager later said this was one of the smoothest projects he had ever worked on—even though they discovered during execution that the existing technical drawings weren’t accurate. Bos Nieuwerkerk handled it flawlessly. But I wouldn’t have expected anything less.”
About Sidney Bakker
Sidney Bakker studied Chemical Engineering at Delft University of Technology. He started his career as a Project Engineer in the world of pumps. “Often, when a client said their pump had failed, the real issue turned out to be how the piping was installed before and after the pump. We’d fix that—and from then on, they’d ask us to take care of the entire installation.” At engineering firm Bilfinger Tebodin, he did more of the same as a Project Manager, just with a few extra zeroes in the budget. For the past year and a half, Sidney has worked as an independent consultant in project communication and management. “In our industry, we do everything to deliver the project, but we often forget to communicate and promote it properly to get people excited. Over the past 25 years, I’ve developed various tools to keep stakeholders engaged using photos, videos and one-pagers. A short video about the project’s progress, sent to headquarters, often has more impact than a lengthy report.”