FAQ
Veelgestelde vragen
FLUE GAS SYSTEMS
The height of a chimney is determined by factors such as deposition and dispersion, which means the dilution of process gases in the atmosphere. Volume flow and environmental requirements play a role as well. What mechanical strength is required depends on the height, with wind zones and earthquake-prone areas being normative for the design.
In Europe, it is a legal requirement that steel structures, including chimneys, comply with the CPR (Construction Products Regulation) in areas such as safety and environment. The requirements for steel structures are laid down in European Standard EN1090-1. The rules for structural design are given in the Eurocode, e.g. EN-1991 (loads), EN-1993 and EN 1090-2 (steel structures), EN-1998 (earthquakes) and other European standards. To prove that all requirements are met, a CE mark must be affixed to the chimney by the manufacturer. The manufacturer may only do so after EN 13084-7, EN 3832-2 and ISO 9001 certification has been granted. In addition, the manufacturer must be FPC-certified to demonstrate that a control and quality management system is in place. They must also be able to issue a Declaration of Performance (DoP).
Factories and plants are not permitted to cause noise pollution for employees and nearby residents. Companies often have a permit that specifies the maximum noise production. In systems with fans, noise occurs on both the suction and discharge sides. This noise can travel outside or back into the production area through chimneys or ducts. Noise pollution is thus reduced by taking noise mitigation measures that address both source and radiated noise.
Yes, depending on the location of the business, chimneys may need to be fitted with warning lights or red and white stripes. This is related to nearby airport approach routes. For chimneys higher than 100 metres, notification to the ILT (Dutch Inspectorate for the Environment and Transport) is mandatory.
It depends on the situation. Insulation may be needed to prevent flue gas cooling and corrosion, to reduce radiation noise or for personal protection if people might come near the installation and ducts (according to Article 7.9 of the Dutch Occupational Health and Safety Decree). In addition, insulation can be applied to make optimal use of residual heat from processes in subsequent (post-combustion) processes, contributing to lower energy consumption.
A chimney is a dynamically loaded structure and must be inspected regularly according to ISO 13084-9. We recommend carrying out an inspection every two years. This is essential for the safety of the site and to ensure the continuity of operations. In a world with increasing legal requirements, regular inspections provide companies with peace of mind.
Yes, the use of work baskets is permitted. In collaboration with our external senior safety expert and certified occupational health and safety specialist, we have developed a mounting and work basket plan in accordance with State Gazette 645 (2021) and the Dutch Working Conditions Decree 7.23d. We report this in advance to the Netherlands Labour Authority. This ensures that our technicians can work safely and in compliance with the regulations.
Turnkey means we manage the entire project from start to finish, including the coordination of all the suppliers we engage: chimneys, fans, steel structures, measurement and control technology, silencers, foundations and, if possible, heat recovery and integration. You get one contact person who coordinates everything, so you don’t have to worry. We ensure that the project is completed on schedule and within budget.
HEAT RECOVERY
The main purpose of heat recovery is to improve the energy efficiency of your process or plant. This leads to lower gas consumption, reduced CO2 emissions and lower operating costs. It also reduces your carbon footprint and helps you meet energy-saving obligations, often with attractive payback periods.
The potential for heat recovery depends on two factors: the amount of heat available and the extent to which it can be reused in your process or elsewhere in the plant. Financial attractiveness is influenced by factors such as temperatures, flow rates, operating hours, energy prices and internal distances. With our Heat Recovery Scan, we can analyse your situation and quickly determine whether heat recovery is of interest to you.
Residual heat can be used for much more than just building heating. Think preheating combustion or drying air, heating cleaning water, or other applications where central heating or a steam boiler is being used. During our Heat Recovery Scan, we will help you determine what application is most suitable for your situation.
To recover heat from corrosive or contaminating flue gas, it is important to pay close attention to cooling, as condensation of acids or accumulation of dirt may occur. This requires careful design of the heat exchanger. We offer polymer heat exchangers that are resistant to acids, making them suitable for this type of flue gas.
Heat recovery has minimal impact on your process. With over 15 years of experience in heat recovery, we guarantee that your existing process will continue undisturbed as much as possible, preferably by installing a bypass for the heat exchanger. We work closely with you to minimise the downtime required during installation.
In collaboration with our sister company Heat Matrix, Bos Nieuwerkerk offers turnkey heat recovery solutions. Our process consists of four steps: a Heat Recovery Scan, the heat integration design, realisation of the system, and service and maintenance. This ensures that you are completely unburdened and the system performs optimally.
ABOUT OUR WORKING METHOD
We prefer to be at the table as early on as possible. This allows us to help think of smart solutions at an early stage and contribute to the performance of all parties involved. With over 50 years of experience, we have a suitable solution for (almost) every question.
We use advanced technology, such as parametric design models and 3D scanning, to optimise our designs and minimise error margins. Our in-house production and cooperation with established partners ensure strict quality control.
Our parametric design model is based on an overcomplete model of a flue gas system, which includes all possible components. By entering all the relevant parameters for a project, the required elements are revealed automatically and at lightning speed, resulting in an efficient design, accurate to the millimetre. Our parametric design model is the result of years of research and development.
At the start of a project, we make a 3D scan of the site to gain an accurate understanding of the building, its dimensions, obstacles and support options. This scan forms the foundation for the engineering process and provides a digital representation of the final design. In addition, the 3D scan is a reliable source for permit applications, a guideline for technical services, and guarantees a reliable production process and an error-free final product.
We manufacture many components ourselves, such as chimneys, ducts and critical parts like vibration dampers. When outsourcing manufacturing to our partners, this is always done under the supervision of our engineers. Our in-house manufacturing is highly appreciated by our clients.
We attach great importance to keeping to our agreements. We are open and transparent about what we can offer and we only promise what we can deliver. This is what our customers value most about us.
ABOUT BOS NIEUWERKERK
Bos Nieuwerkerk was founded in 1973 and has evolved into a specialist in chimney technology. Through the acquisition of Heat Matrix and cooperation with specialised partners, we have built a strong market position in turnkey flue gas and heat recovery systems.
Our core philosophy is: business is business, but above all, business is people. We put people at the heart of everything we do. We believe in fair, equal business and honouring agreements. Our customers appreciate this way of working: 85% of our orders come from repeat clients, and they are many.
Yes, we have been working for years with trusted partners who, like us, strive to provide industrial companies with the best products. We look for partners who not only deliver quality, but also contribute to our clients’ sustainability ambitions.
Yes, Bos Nieuwerkerk mainly sponsors charities and initiatives in the Zuidplas municipality. We like to support local associations and projects, both in kind and with financial contributions. Does your association or initiative need support? Please feel free to get in touch.
BN/HM Groep combines the experience of Heat Matrix and Bos Nieuwerkerk to realise turnkey flue gas systems and heat recovery solutions. Other companies can join the group in the future to work together towards smarter and better industry.
CAREERS
At Bos Nieuwerkerk, we believe that work is more than a job. It offers opportunities for personal development and fun, while employees are part of a growing family. Personal attention is key, and each employee is seen as a valuable team member.
We invest in employees by nurturing their skills and guiding them with education, training and coaching. Whether you are an experienced professional or just starting out, we offer an environment where you can grow, learn and celebrate successes together.
Our process consists of four steps: analysis and advice, engineering, realisation and service. Different disciplines are active in each step of the process: sales people, project and process engineers, project managers, work planners, structural engineers, welders and assembly workers. Are you interested in a particular position or internship? Take a look at our vacancies or drop by for a chat.
We nurture a family business culture where job satisfaction, caring for each other and personal growth are key. Employees often have a long track record, which ensures strong mutual cooperation and a sense of responsibility.
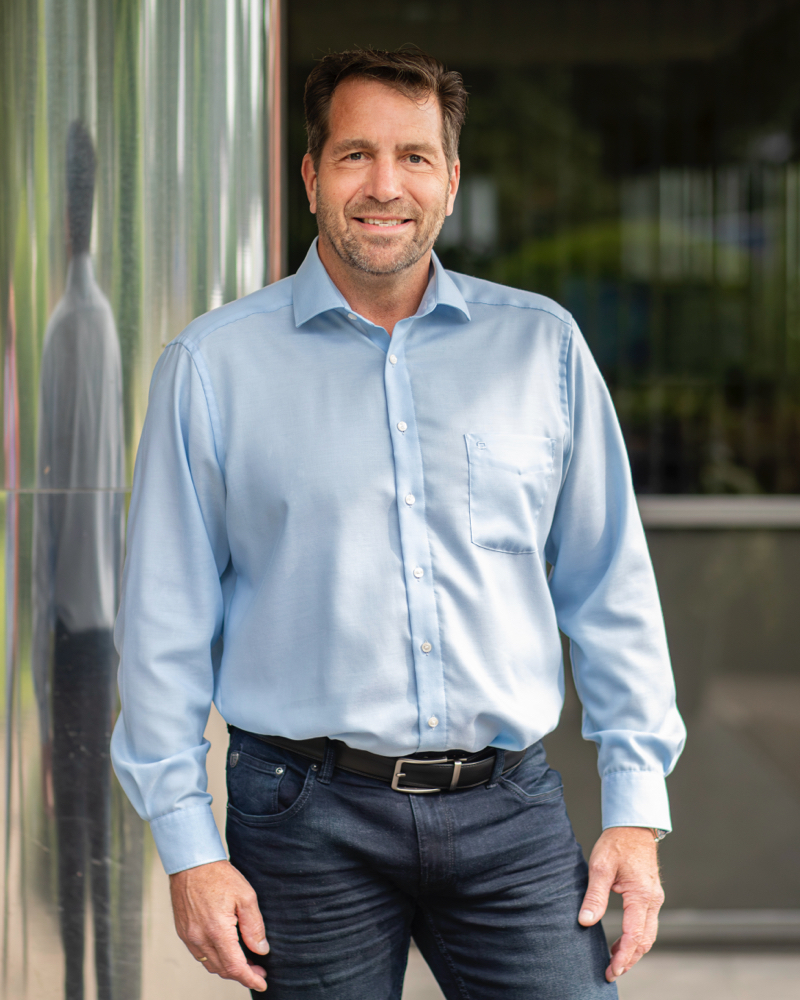
Contact
Work together?
With our knowledge and no-nonsense approach, we have the answer to your question with a keen eye for feasibility, planning and cost considerations. Please get in touch with Cor de Leeuw.